Alloys Could Reduce Costs For Chemical, Petrochemical Industries
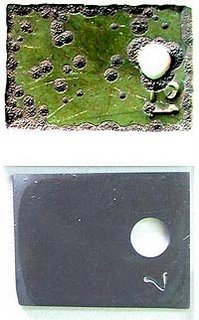
Materials developed by scientists at Argonne National Laboratory could provide large cost and energy savings to the chemical and petrochemical industries.
The new alloy materials — which won an R&D 100 award from R&D magazine as one of the top 100 scientific and technological innovations in the world during 2005 — are resistant to metal dusting, a type of degradation that occurs at elevated temperatures in hydrocarbon-containing atmospheres in which carbon activity is high.
Such environments are prevalent in chemical and petrochemical industries such as hydrogen-, methanol- and ammonia-reformers and in synthesis gas production plants. The degradation of metallic component materials into powder and the resulting damage make it difficult to maintain equipment used in these industries. Currently, almost all commercial alloys degrade by metal dusting corrosion.
"More than 50 years of previous research could not solve this problem," says Argonne researcher Ken Natesan. "The only available solution was to quench the high-temperature gases by lowering the working temperature, which results in energy loss and decreased product yield."
In a study lasting several years, Natesan and Argonne researcher Zuotao Zeng established the role of carbon deposition in the mechanism leading to initiation and propagation of metal dusting. The work was conducted at both atmospheric and high pressures and simulated the gas chemistry — including the high steam content — prevalent in reformer environments.
This led to the development of alloys that resist this type of degradation and can be used to build equipment for the chemical and petrochemical industries. The Argonne-developed alloys performed significantly better than the currently available commercial alloys when tested in the metal dusting environment because they develop oxide scales that resist carbon attack. For example, an Argonne-developed alloy was still smooth and without pits after exposure to the same metal dusting environment for 5,700 hours at 593 degrees Celsius. Commercial alloys tested under the same conditions developed large pits.
Application of the Argonne-developed alloys in the future may enable a complete redesign of reforming systems with improved efficiency. Using these materials to build such industrial equipment could save 500 trillion Joules of energy each day, which is equivalent to 13 million standard cubic meters of natural gas each day. Financially, this innovation could save $500 million to $1.3 billion per year in the hydrogen industry alone and could increase industrial productivity by enabling machinery to function with fewer maintenance shutdowns. Such savings will become increasingly important as hydrogen is used more as a source of energy.
While the initial application of the Argonne-developed alloys is in hydrogen and synthesis gas production plants, they can also be used for components such as waste heat boilers and gas bypass lines exposed to metal dusting environments in methanol and ammonia reformer plants.
They can also be effective in gas-to-liquid plants in which natural gas is converted into liquid fuels.
0 Comments:
Post a Comment
Subscribe to Post Comments [Atom]
<< Home